A porosidade, descontinuidades do tipo cavidade formadas pelo aprisionamento de gás durante a solidificação, é um defeito comum, mas incômodo, na soldagem MIG e com diversas causas. Ele pode aparecer em aplicações semiautomáticas ou robóticas e requer remoção e retrabalho em ambos os casos, levando a tempo de inatividade e aumento de custos.
A principal causa da porosidade na soldagem do aço é o nitrogênio (N2), que se envolve na poça de soldagem. Quando a poça de líquido esfria, a solubilidade do N2 é significativamente reduzida e o N2 sai do aço fundido, formando bolhas (poros). Na soldagem galvanizada/galvanneal, o zinco evaporado pode ser misturado na poça de soldagem e, se não houver tempo suficiente para escapar antes que a poça se solidifique, ele forma porosidade. Na soldagem do alumínio, toda a porosidade é causada pelo hidrogênio (H2), da mesma forma que o N2 funciona no aço.
A porosidade da soldagem pode aparecer externa ou internamente (frequentemente chamada de porosidade subterrânea). Também pode se desenvolver em um único ponto da solda ou ao longo de todo o comprimento, resultando em soldas fracas.
Saber como identificar algumas das principais causas da porosidade e como resolvê-las rapidamente pode ajudar a melhorar a qualidade, a produtividade e os resultados financeiros.
Má cobertura de gás de proteção
A má cobertura do gás de proteção é a causa mais comum de porosidade na soldagem, pois permite que gases atmosféricos (N2 e H2) contaminem a poça de fusão. A falta de cobertura adequada pode ocorrer por vários motivos, incluindo, entre outros, baixa vazão do gás de proteção, vazamentos no canal de gás ou excesso de fluxo de ar na célula de solda. Velocidades de viagem muito rápidas também podem ser as culpadas.
Se um operador suspeitar que o fluxo insuficiente está causando o problema, tente ajustar o medidor de fluxo de gás para garantir que a taxa seja adequada. Ao usar um modo de transferência por pulverização, por exemplo, um fluxo de 35 a 50 pés cúbicos por hora (cfh) deve ser suficiente. A soldagem em amperagens mais altas requer um aumento na vazão, mas é importante não definir a vazão muito alta. Isso pode resultar em turbulência em alguns projetos de armas que interrompem a cobertura do gás de proteção.
É importante observar que pistolas projetadas de forma diferente têm características diferentes de fluxo de gás (veja dois exemplos abaixo). O “ponto ideal” da vazão de gás para o projeto superior é muito maior do que o do projeto inferior. Isto é algo que um engenheiro de soldagem precisa considerar ao configurar a célula de solda.
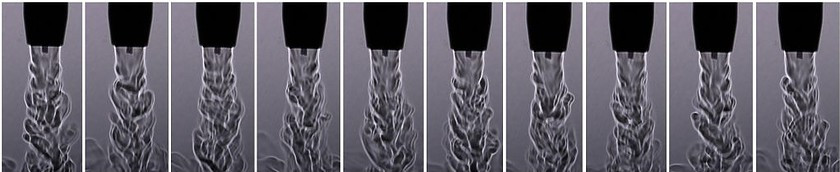
O projeto 1 mostra um fluxo suave de gás na saída do bico
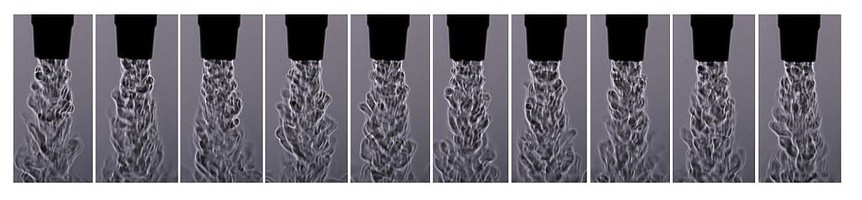
O Projeto 2 mostra fluxo turbulento de gás na saída do bocal.
Verifique também se há danos na mangueira de gás, nas conexões e nos conectores, bem como nos anéis de vedação no pino de alimentação da pistola de soldagem MIG. Substitua conforme necessário.
Ao usar ventiladores para resfriar operadores ou peças em uma célula de soldagem, tome cuidado para que eles não estejam apontados diretamente para a área de soldagem, onde poderiam interromper a cobertura de gás. Coloque uma tela na célula de solda para proteger do fluxo de ar externo.
Retoque o programa em aplicações robóticas para garantir que haja uma distância adequada entre a ponta e a obra, que normalmente é de ½ a 3/4 de polegada, dependendo do comprimento desejado do arco.
Por último, diminua a velocidade de deslocamento se a porosidade persistir ou consulte um fornecedor de pistola MIG para obter diferentes componentes frontais com melhor cobertura de gás
Contaminação de metais básicos
A contaminação por metais básicos é outra razão pela qual ocorre a porosidade – desde óleo e graxa até carepa e ferrugem. A umidade também pode estimular essa descontinuidade, especialmente na soldagem de alumínio. Esses tipos de contaminantes normalmente levam à porosidade externa que é visível para o operador. O aço galvanizado é mais sujeito à porosidade subterrânea.
Para combater a porosidade externa, certifique-se de limpar completamente o material de base antes da soldagem e considere o uso de um fio de solda com núcleo metálico. Este tipo de fio possui níveis mais elevados de desoxidantes do que o fio sólido, por isso é mais tolerante a quaisquer contaminantes remanescentes no material de base. Sempre armazene esses e quaisquer outros fios em uma área seca e limpa, com temperatura semelhante ou um pouco mais alta que a da planta. Isso ajudará a minimizar a condensação que poderia introduzir umidade na poça de fusão e causar porosidade. Não armazene os fios em um armazém frio ou ao ar livre.
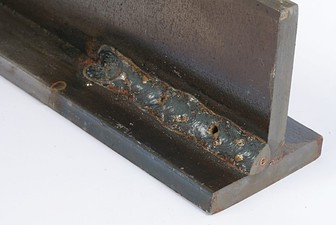
A porosidade, descontinuidades do tipo cavidade formadas pelo aprisionamento de gás durante a solidificação, é um defeito comum, mas incômodo, na soldagem MIG e com diversas causas.
Ao soldar aço galvanizado, o zinco vaporiza a uma temperatura mais baixa do que o aço derrete, e velocidades rápidas de deslocamento tendem a fazer com que a poça de fusão congele rapidamente. Isso pode reter o vapor de zinco no aço, resultando em porosidade. Combata esta situação monitorando as velocidades de deslocamento. Novamente, considere um fio com núcleo de metal especialmente projetado (fórmula de fluxo) que promova o escape de vapor de zinco da poça de soldagem.
Bicos entupidos e/ou subdimensionados
Bicos entupidos e/ou subdimensionados também podem causar porosidade. Respingos de soldagem podem se acumular no bico e na superfície do bico de contato e do difusor, restringindo o fluxo do gás de proteção ou tornando-o turbulento. Ambas as situações deixam a poça de fusão com proteção inadequada.
Para agravar esta situação está um bico que é muito pequeno para a aplicação e mais propenso a um acúmulo maior e mais rápido de respingos. Bicos menores podem proporcionar melhor acesso à junta, mas também obstruem o fluxo de gás devido à menor área de seção transversal permitida para o fluxo de gás. Tenha sempre em mente a variável entre o bico de contato e a saliência (ou recesso) do bico, pois esse pode ser outro fator que afeta o fluxo do gás de proteção e a porosidade na seleção do bico.
Pensando nisso, certifique-se de que o bico seja grande o suficiente para a aplicação. Normalmente, aplicações com alta corrente de soldagem usando tamanhos de fio maiores requerem um bico com diâmetros maiores.
Em aplicações de soldagem semiautomática, verifique periodicamente se há respingos de soldagem no bico e remova-os com alicates de soldador (soldadores) ou substitua o bico se necessário. Durante esta inspeção, confirme se a ponta de contato está em bom estado e se o difusor de gás possui portas de gás desobstruídas. Os operadores também podem usar composto anti-respingos, mas devem tomar cuidado para não mergulhar o bico no composto muito ou por muito tempo, pois quantidades excessivas do composto podem contaminar o gás de proteção e danificar o isolamento do bico.
Em uma operação de soldagem robótica, invista em uma estação de limpeza de bicos ou alargador para combater o acúmulo de respingos. Este periférico limpa o bocal e o difusor durante as pausas rotineiras da produção para que não afete o tempo do ciclo. As estações de limpeza de bicos destinam-se a funcionar em conjunto com um pulverizador anti-respingos, que aplica uma fina camada do composto nos componentes frontais. Muito ou pouco fluido anti-respingos pode resultar em porosidade adicional. Adicionar jato de ar a um processo de limpeza de bicos também pode ajudar a limpar respingos soltos dos consumíveis.
Mantendo a qualidade e a produtividade
Tendo o cuidado de monitorar o processo de soldagem e conhecer as causas da porosidade, é relativamente simples implementar soluções. Isso pode ajudar a garantir maior tempo de arco ligado, resultados de qualidade e mais peças boas circulando na produção.
Horário da postagem: 02 de fevereiro de 2020