O equipamento de soldagem Xinfa possui características de alta qualidade e baixo preço. Para obter detalhes, visite:Fabricantes de soldagem e corte - Fábrica e fornecedores de soldagem e corte na China (xinfatools.com)
4. Poços de arco
É um fenômeno de deslizamento descendente no final da solda, que não só enfraquece a resistência da solda, mas também causa trincas durante o processo de resfriamento.
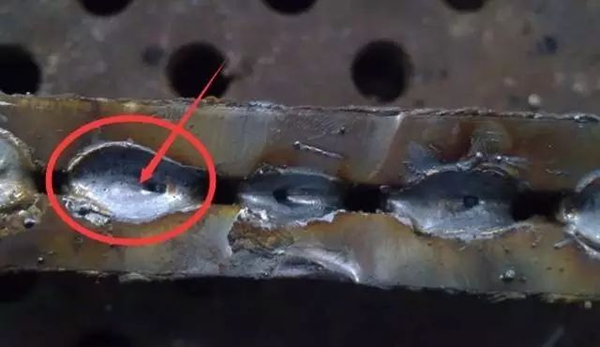
4.1 Causas:
Principalmente, o tempo de extinção do arco é muito curto no final da soldagem ou a corrente usada na soldagem de placas finas é muito grande.
4.2 Medidas preventivas:
Terminada a soldagem, faça com que o eletrodo permaneça por um curto período de tempo ou faça vários movimentos circulares. Não interrompa o arco repentinamente para que haja metal suficiente para preencher a poça de fusão. Garanta a corrente apropriada durante a soldagem. Os componentes principais podem ser equipados com placas de início de arco para conduzir o arco para fora da soldagem.
5. Inclusão de escória
5.1 Fenômeno: Inclusões não metálicas como óxidos, nitretos, sulfetos, fosfetos, etc. são encontradas na solda por meio de ensaios não destrutivos, formando uma variedade de formatos irregulares, sendo os mais comuns em formato de cone, formato de agulha e outros. inclusões de escória. As inclusões de escória nas soldas metálicas reduzirão a plasticidade e a tenacidade das estruturas metálicas e também aumentarão a tensão, resultando em fragilidade a frio e a quente, que é fácil de rachar e danificar os componentes.
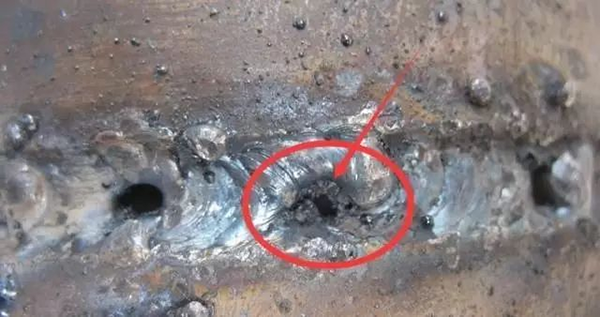
5.2 Razões:
5.2.1 O metal base da solda não é limpo adequadamente, a corrente de soldagem é muito pequena, o metal fundido solidifica muito rapidamente e a escória não tem tempo de flutuar.
5.2.2 A composição química do metal base de soldagem e da haste de soldagem é impura. Se houver vários componentes, como oxigênio, nitrogênio, enxofre, fósforo, silício, etc. na poça fundida durante a soldagem, inclusões de escória não metálica são facilmente formadas.
5.2.3 O soldador não tem habilidade na operação e o método de transporte da haste é inadequado, fazendo com que a escória e o ferro fundido fiquem misturados e inseparáveis, o que dificulta a flutuação da escória.
5.2.4 O ângulo da ranhura da solda é pequeno, o revestimento da haste de soldagem cai em pedaços e não é derretido pelo arco; durante a soldagem multicamadas, a escória não é limpa adequadamente e a escória não é removida a tempo durante a operação, o que é uma causa da inclusão de escória.
5.3 Medidas de prevenção e controle
5.3.1 Utilize hastes de soldagem apenas com bom desempenho no processo de soldagem, e o aço soldado deve atender aos requisitos dos documentos de projeto.
5.3.2 Selecione parâmetros razoáveis do processo de soldagem por meio da avaliação do processo de soldagem. Preste atenção na limpeza da ranhura de soldagem e da borda. A ranhura da haste de soldagem não deve ser muito pequena. Para soldas multicamadas, a escória de soldagem de cada camada de solda deve ser removida com cuidado.
5.3.3 Ao utilizar eletrodos ácidos, a escória deve ficar atrás da poça de fusão; ao utilizar eletrodos alcalinos para soldar costuras angulares verticais, além de selecionar corretamente a corrente de soldagem, deve-se utilizar soldagem por arco curto. Ao mesmo tempo, o eletrodo deve ser movido corretamente para fazer com que ele balance adequadamente para que a escória flutue na superfície.
5.3.4 Use pré-aquecimento antes da soldagem, aquecimento durante a soldagem e isolamento após a soldagem para esfriar lentamente e reduzir inclusões de escória.
6. Porosidade
6.1 Fenômeno: O gás absorvido no metal de solda fundido durante o processo de soldagem não tem tempo de ser descarregado da poça de fusão antes do resfriamento e permanece dentro da solda para formar furos. De acordo com a localização dos poros, eles podem ser divididos em poros internos e externos; de acordo com a distribuição e formato dos defeitos dos poros, a presença de poros na solda reduzirá a resistência da solda e também produzirá concentração de tensões, aumentará a fragilidade em baixas temperaturas, tendência à trinca térmica, etc.
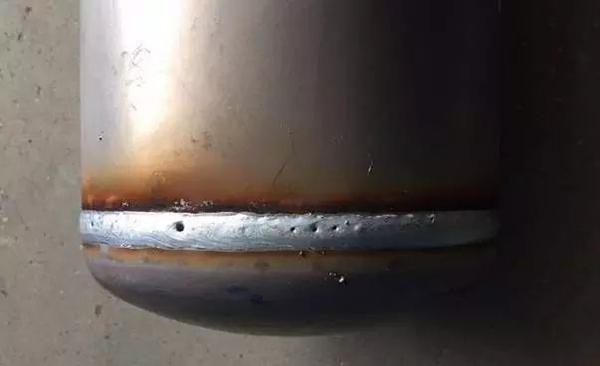
6.2 Razões
6.2.1 A qualidade da haste de soldagem em si é ruim, a haste de soldagem está úmida e não seca de acordo com os requisitos especificados; o revestimento da haste de soldagem está deteriorado ou descascado; o núcleo de soldagem está enferrujado, etc.
6.2.2 Existe gás residual na fundição do material original; a haste de soldagem e a soldagem ficam manchadas com impurezas como ferrugem e óleo e, durante o processo de soldagem, é gerado gás devido à gaseificação em alta temperatura.
6.2.3 O soldador não tem habilidade em tecnologia de operação ou tem visão deficiente e não consegue distinguir entre ferro fundido e revestimento, de modo que o gás do revestimento se mistura com a solução metálica. A corrente de soldagem é muito grande, tornando a haste de soldagem vermelha e reduzindo o efeito de proteção; o comprimento do arco é muito longo; a tensão da fonte de alimentação flutua muito, fazendo com que o arco queime instável, etc.
6.3 Medidas de prevenção e controle
6.3.1 Selecione varetas de solda qualificadas e não use varetas de solda com revestimentos rachados, descascados, deteriorados, excêntricos ou muito enferrujados. Limpe as manchas de óleo e ferrugem perto da solda e na superfície da haste de soldagem.
6.3.2 Escolha a corrente apropriada e controle a velocidade de soldagem. Pré-aqueça a peça de trabalho antes de soldar. Ao final ou pausa da soldagem, o arco deve ser retirado lentamente, o que contribui para desacelerar a velocidade de resfriamento da poça fundida e a descarga do gás na poça fundida, evitando a ocorrência de defeitos de poros.
6.3.3 Reduza a umidade do local de operação de soldagem e aumente a temperatura do ambiente operacional. Ao soldar ao ar livre, se a velocidade do vento atingir 8m/s, chuva, orvalho, neve, etc., medidas eficazes como quebra-ventos e coberturas devem ser tomadas antes das operações de soldagem.
7. Falha na limpeza de respingos e escória de soldagem após a soldagem
7.1 Fenômeno: Este é o problema mais comum, que não é apenas desagradável, mas também muito prejudicial. Respingos fusíveis aumentarão a estrutura endurecida da superfície do material e é fácil produzir defeitos como endurecimento e corrosão local.
7.2 Razões
7.2.1 A película medicinal do material de soldagem está úmida e deteriorada durante o armazenamento, ou a haste de soldagem selecionada não corresponde ao material original.
7.2.2 A seleção do equipamento de soldagem não atende aos requisitos, o equipamento de soldagem AC e DC não corresponde aos materiais de soldagem, o método de conexão de polaridade da linha secundária de soldagem está incorreto, a corrente de soldagem é grande, a borda da ranhura de solda é contaminado por detritos e manchas de óleo, e o ambiente de soldagem não atende aos requisitos de soldagem.
7.2.3 O operador não é qualificado e não opera e protege de acordo com os regulamentos.
7.3 Medidas de prevenção e controle
7.3.1 Selecione o equipamento de soldagem apropriado de acordo com o material base da soldagem.
7.3.2 O eletrodo de soldagem deve possuir equipamento de secagem e temperatura constante, devendo haver desumidificador e ar condicionado na sala de secagem, que não esteja a menos de 300mm do solo e da parede. Estabeleça um sistema para receber, enviar, usar e guardar hastes de soldagem (especialmente para vasos de pressão).
7.3.3 Limpe a borda da solda para remover umidade, manchas de óleo e ferrugem dos detritos. Durante a estação chuvosa de inverno, um galpão de proteção é construído para garantir o ambiente de soldagem.
7.3.4 Antes de soldar metais não ferrosos e aço inoxidável, revestimentos protetores podem ser aplicados aos materiais originais em ambos os lados da solda para proteção. Você também pode escolher varetas de solda, varetas de solda com revestimento fino e proteção de argônio para eliminar respingos e reduzir a escória.
7.3.5 A operação de soldagem requer limpeza oportuna da escória de soldagem e proteção.
8. Cicatriz de arco
8.1 Fenômeno: Devido à operação descuidada, a haste de soldagem ou cabo de soldagem entra em contato com a soldagem, ou o fio terra entra em contato ruim com a peça de trabalho, causando um arco por um curto período de tempo, deixando uma cicatriz de arco na superfície da peça de trabalho.
8.2 Motivo: O operador de soldagem elétrica é descuidado e não toma medidas de proteção e manutenção das ferramentas.
8.3 Medidas preventivas: Os soldadores devem verificar regularmente o isolamento do fio do cabo de soldagem e do fio terra utilizado e envolvê-los a tempo se estiverem danificados. O fio terra deve ser instalado de forma firme e confiável. Não inicie um arco fora da solda durante a soldagem. O grampo de soldagem deve ser colocado isolado do material base ou pendurado de forma adequada. Corte a fonte de alimentação a tempo quando não estiver soldando. Se forem encontrados arranhões de arco, eles devem ser polidos com um rebolo elétrico a tempo. Porque em peças com requisitos de resistência à corrosão, como o aço inoxidável, as cicatrizes do arco se tornarão o ponto de partida da corrosão e reduzirão o desempenho do material.
9. Cicatrizes de solda
9.1 Fenômeno: A não limpeza das cicatrizes de solda após a soldagem afetará a qualidade macroscópica do equipamento e o manuseio inadequado também causará rachaduras superficiais.
9.2 Causa: Durante a produção e instalação de equipamentos não padronizados, o posicionamento dos acessórios de soldagem é causado quando são removidos após a conclusão.
9.3 Medidas preventivas: Os dispositivos de elevação utilizados no processo de montagem devem ser polidos com rebolo para ficarem nivelados com o material original após a remoção. Não use uma marreta para derrubar os acessórios para evitar danificar o material original. Poços de arco e arranhões muito profundos durante a soldagem elétrica devem ser reparados e polidos com um rebolo para ficarem nivelados com o material original. Contanto que você preste atenção durante a operação, esse defeito pode ser eliminado.
10. Penetração incompleta
10.1 Fenômeno: Durante a soldagem, a raiz da solda não está completamente fundida com o material base ou o material base e o material base são parcialmente soldados de forma incompleta. Este defeito é denominado penetração incompleta ou fusão incompleta. Reduz as propriedades mecânicas da junta e causará concentração de tensões e fissuras nesta área. Na soldagem, nenhuma solda pode ter penetração incompleta.
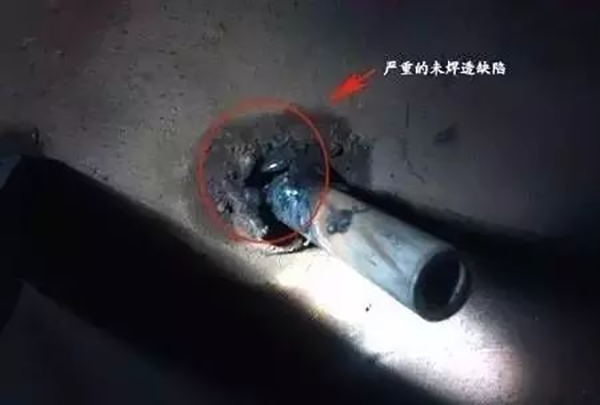
10.2 Causas
10.2.1 A ranhura não é processada de acordo com os regulamentos, a espessura da borda romba é muito grande e o ângulo da ranhura ou a folga do conjunto é muito pequeno.
10.2.2 Na soldagem bilateral, a raiz posterior não é totalmente limpa ou as laterais da ranhura e a solda intercamada não são limpas, de forma que óxidos, escórias, etc.
10.2.3 O soldador não tem habilidade na operação. Por exemplo, quando a corrente de soldagem é muito grande, o material de base não derreteu, mas a haste de soldagem derreteu, de modo que o material de base e o metal depositado na haste de soldagem não são fundidos; quando a corrente é muito pequena; a velocidade da haste de soldagem é muito rápida, o material de base e o metal depositado na haste de soldagem não podem ser bem fundidos; na operação, o ângulo da haste de soldagem está incorreto, o derretimento é desviado para um lado ou ocorrerá o fenômeno de sopro durante a soldagem, o que causará penetração incompleta onde o arco não pode atuar.
10.3 Medidas preventivas
10.3.1 Processe e monte a folga de acordo com o tamanho da ranhura especificado no desenho do projeto ou na norma de especificação.
Horário da postagem: 28 de julho de 2024